Esta es la copa de vino impresa en 3D más pequeña del mundo, dicen científicos suecos – Ars Technica
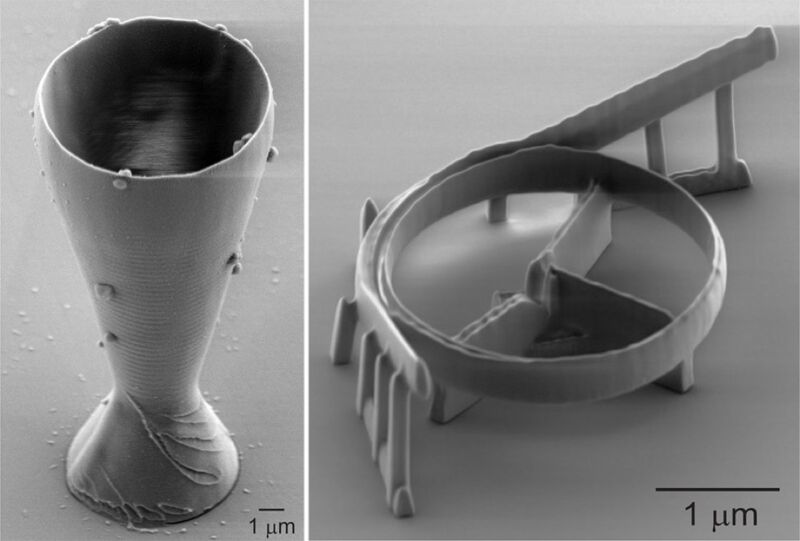
Instituto Real de Tecnología KTH
Un equipo de científicos suecos ha desarrollado una nueva técnica de impresión 3D para vidrio de sílice que agiliza un complicado proceso intensivo en energía. Como prueba de concepto, imprimieron en 3D la copa de vino más pequeña del mundo (hecha de vidrio real) con un borde más pequeño que el ancho de un cabello humano, así como un resonador óptico para sistemas de telecomunicaciones de fibra óptica, una de varias aplicaciones potenciales para Componentes de vidrio de sílice impresos en 3D. Describieron su nuevo método en un artículo reciente en la revista Nature Communications.
“La columna vertebral de Internet se basa en fibras ópticas de vidrio”, dijo la coautora Kristinn Gylfason del Instituto Real de Tecnología KTH de Estocolmo. «En estos sistemas, se necesitan todo tipo de filtros y acopladores que ahora se pueden imprimir en 3D con nuestra técnica. Esto abre muchas posibilidades nuevas».
El vidrio de sílice (es decir, el dióxido de silicio amorfo) es un material que sigue siendo un desafío para la impresión 3D, particularmente a microescala, según los autores, aunque varios métodos buscan abordar este desafío, incluida la estereolitografía, la escritura directa con tinta y el procesamiento de luz digital. . Incluso esos solo lograron alcanzar tamaños de características del orden de varias decenas de micrómetros, más un estudio 2021 que reportó resolución a nanoescala.
Pero todos usan sol-gel procesos que involucran diferentes mezclas orgánicas cargadas con nanopartículas de sílice. Por lo tanto, las estructuras impresas finales están compuestas con muchos materiales orgánicos, por lo tanto, sin las propiedades más deseadas del vidrio de sílice (es decir, estabilidad térmica y química, dureza, transparencia óptica en una amplia gama de longitudes de onda). Requiere un paso de sinterización adicional a altas temperaturas de alrededor de 1200 ° Celsius (2192 ° F) durante varias horas para eliminar los residuos orgánicos y lograr estas propiedades. Este paso adicional que consume mucha energía limita severamente las aplicaciones potenciales, ya que solo se pueden usar materiales de sustrato que puedan soportar temperaturas tan altas. Algunos enfoques también requieren ensamblar estructuras impresas en 3D en una forma final, lo cual es un desafío a escala micrométrica.
Al desarrollar su técnica alternativa para la impresión 3D de vidrio de sílice, Gylfason y otra. se volvió hacia hidrogeno de silsesquioxano (HSQ), un material inorgánico similar a la sílice y puede ser modelado por haces de electrones, haces de iones y ciertas longitudes de onda de luz ultravioleta. Una gran ventaja es que su método no se basa en compuestos orgánicos para actuar como fotoiniciadores o aglutinantes que permanecen en el sustrato, como en la estereolitografía o la escritura con tinta directa. En cambio, su método se basa en la reticulación directa de HSQ inorgánico.
El proceso tiene tres pasos principales. Primero, arrojaron HSQ disuelto en solventes orgánicos sobre un sustrato. Después de que el HSQ se seque, trazan la forma 3D deseada utilizando un rayo láser de subpicosegundos enfocado. Finalmente, cualquier HSQ no expuesto se disuelve con la aplicación práctica de una solución de hidróxido de potasio. La espectroscopia Raman de las microestructuras impresas mostró todas las características esperadas para el vidrio de sílice.
Sin embargo, también había rastros de hidrógeno y carbono residuales. Para aplicaciones que requieren un vidrio de sílice más puro, los residuos orgánicos se pueden eliminar recociendo los marcos a 900 ° Celsius (1652 ° F), un paso adicional, garantizado, pero a una temperatura mucho más baja que el paso adicional habitual de sinterización. A partir de entonces, el espectro de las estructuras coincidió con el de un sustrato de vidrio de sílice fundido comercial. Si bien el recocido de las microestructuras impresas en 3D puede hacer que se encojan o se distorsionen, los autores descubrieron que la contracción máxima de sus estructuras de vidrio de sílice era de alrededor del 6 %, en comparación con el 16 % y el 56 % de los objetos de vidrio fabricados con estereolitografía y métodos directos de escritura con tinta. .
Además de la diminuta copa de vino y el resonador óptico de prueba de concepto, los autores imprimieron una versión diminuta del logotipo de KTH, una espiral cónica y en voladizo, así como una punta de fibra óptica de vidrio de sílice. Creen que su método también podría usarse para fabricar lentes personalizados para dispositivos médicos y microrobots. Recubrir las microestructuras impresas en 3D con nanodiamantes o nanopartículas ferrosas podría permitir una mayor adaptación de las propiedades para la integración de la fotónica cuántica híbrida o la eliminación magnética del control de movimiento de las estructuras, respectivamente.
“Las preocupaciones al integrar métodos de impresión 3D a menudo son diferentes para diferentes aplicaciones”, dijo el coautor Po-Han Huang, estudiante de posgrado en KTH. «Si bien todavía se necesita la optimización de nuestro método para diferentes aplicaciones, creemos que nuestro método presenta un avance importante y necesario para que la impresión 3D de vidrio se use en escenarios prácticos».
DOI: Comunicaciones de la naturaleza, 2023. 10.1038/s41467-023-38996-3 (Sobre los DOI).